- 기사등록 2018-02-06 16:38:11
차세대 연료전지 개발, 정부지원 시급
■ 기술의 원리
1) 고체산화물 연료전지 개요 및 작동 원리
지르코니아 등의 산화물 세라믹스로 구성된 전해질 소재를 통하여 산소 이온(O2-)이 움직이며, 이 때문에 다른 연료전지보다 고온(600~1,000℃)에서 작동된다. 이러한 산소이온의 움직임은 공기극과 연료극의 산소 분압차에 의하여 발생한다. 이때 화학반응의 전기적 균형을 맞추기 위해 외부 회로를 통해 연료극의 전자가 공기극으로 이동하게 되고 외부 부하를 조절하여 원하는 전류를 얻을 수 있게 된다. SOFC는 연료전지 중 가장 발전효율이 높고, 고온의 배기가스를 이용하여 열병합 발전이 용이한 장점이 있다.
고체산화물 연료전지의 단위셀은 일반적으로 중앙에 가스가 통과하지 못하는 치밀한 구조의 전해질(electrolyte)이 있고, 양쪽에 다공질 구조의 연료극(anode)과 공기극(cathode)이 있으며 그 바깥쪽에 연결재(interconnect)가 있다. 셀의 성능 향상을 위해 이중의 전극 구조를 사용하거나 전극과 전해질 사이에 기능층을 사용하기도 한다. 전해질을 사이에 두고 양 전극에 산소와 수소를 공급해 주면 공기극과 연료극측 간에 산소 분압 차이가 형성되어 전해질을 통해 산소가 이동하려는 구동력이 생기게 된다. 공기극에서는 산소가 전자를 받아 산소이온으로 되어 전해질 막을 통과하여 연료극으로 이동하고 연료극에서는 산소이온이 전자를 방출하고 수소가스와 반응하여 수증기로 된다. 이렇게 방출된 전자를 통해 전기에너지가 발생하게 되며 이 전기에너지를 인출하여 전력을 생산하게 된다. 전해질은 가스를 직접 투과시키지 않기 위해 치밀한 구조를 가져야 하며 산소이온 전도성은 높을수록 좋지만, 전자전도성은 매우 낮아야 한다. 연료극과 공기극은 각각 연료가스와 산소가 잘 확산되어 들어갈 수 있도록 다공질이어야 하며 높은 전자전도성을 지녀야 한다.
각각의 셀 구성 요소들은 다른 전기적 특성 및 미세구조를 요구하며, 이를 구현하기 위한 최적의 소재 및 공정 기술이 요구된다. 각각의 SOFC의 각 구성 재료가 갖춰야 할 주요 요구조건 및 이에 비교적 부합하는 구성 재료들을 <표 3-3-1-1>에 나타내었다. 이와 같은 구조적 및 전기적 특성 외에도, 열사이클에 대한 안정성 확보를 위해 각각의 구성 요소들이 다른 구성요소와 열팽창계수가 일치해야 하며, 장기 안정성 확보를 위해 구성재료 상호 간의 화학반응 및 확산이 없어야 한다. 그러나 현재까지는 이와 같은 요구조건에 완벽하게 부합하는 재료의 개발은 이루어지지 못하고 있으며, 이와 같은 재료들을 SOFC에 사용하기 위한 성능향상과 새로운 재료 개발이 이루어지고 있다.
2) 고체산화물 연료전지의 분류
고체산화물 연료전지는 제작형태에 따라 원통형(tubular type), 평판형(plannar type), 그리고 평관형(flatten tubular)으로 구분할 수 있다. 원통형 셀은 연료가스와 공기를 분리하는 실링 범위가 좁기 때문에 셀 열화 및 운전 안정성에 많은 영향을 미치는 유리 실링재의 영향에서 상대적으로 자유롭고 대형화에 유리한 장점이 있다. 하지만, 셀 내에서 전류의 이동 경로가 길어져 셀의 출력 특성이 저하되고 제조비용 또한 평판형 셀에 비해 상대적으로 높은 것이 단점이다. 반면 평판형 셀의 경우 셀 출력 특성 면에서 상대적으로 유리하다. 두 가지 형태의 셀의 장점을 취합하여 만든 평관형의 셀도 근래 활발하게 연구 응용되어 오고 있다.
다른 분류 방식으로, 셀 제작 시 지지체로 사용하는 셀 구성요소 및 물질을 기준으로 전해질 지지체형(electrolyte-supported type), 음극 지지체형(anode-supported type), 양극 지지체형(cathode-supported type), 그리고 분리판으로 사용되는 금속을 다공질화 하여 지지체로 사용하는 금속지지체형(metal-supported type) 등으로 분류할 수 있다. 전해질 지지체형은 높은 치밀도가 요구되는 전해질을 고온(1,400℃ 내외)에서 상대적으로 두껍게(~300㎛) 제작하여 단독 소결하고, 다공질의 전극 소재를 상대적으로 낮은 공정온도(1,000~1,200℃)에서 소성하여 전해질과 전극의 계면 접합력을 부여하는 공정을 사용한다. 반면 전극을 지지체로 사용할 경우 전해질 두께를 더욱 얇게(~10㎛ 이하) 가져갈 수 있으므로, 전해질의 저항 성분을 크게 낮출 수 있고 결과적으로 높은 출력특성을 얻을 수 있으므로, 최근의 연구 경향은 전극 지지체형, 특히 양극 물질보다 상대적으로 저가인 음극을 지지체로 사용하는 구조에 집중됐다. 그러나 장기안정성 및 신뢰성 면에서 산화환원 반복에 상대적으로 취약한(redox stability) 음극 지지체형에 비해 제조 공정이 간단하고 보다 신뢰성이 높은 전해질 지지형을 다시 주력으로 삼고 제품개발을 하는 업체 및 연구소들도 늘어가고 있는 실정이다(Bloom Energy, 프라운호퍼 IKTS 등). 금속지지형의 경우 모든 셀의 세라믹 구성요소를 박막화 하고 다공질의 금속이 전체 구조를 기계적으로 지지하여 기계적 신뢰성을 극대화한 구조로 제조 공정상의 어려움을 극복할 수 있다면 고체산화물 연료전지의 신뢰성 문제를 해결할 수 있는 훌륭한 대안이 될 것으로 기대된다. <표 3-3-1-2>에 고체산화물 연료전지 형태별 장단점 및 개발회사를 정리하였다.
3) 고체산화물 연료전지 전해질 소재기술
고체산화물 연료전지는 고체산화물의 산소이온 전도특성에 그 원리를 두고 있다. 산소이온 전도가 일어나는 산화물(고체전해질)의 한쪽은 공기(산소분압 ~0.21기압)와 접촉하며, 다른 한쪽은 연료(수소의 경우 일반적으로 ~10-19기압)와 접촉하게 하면 양단의 산소 분압 차이에 의해 산소이온이 이동하게 되고 양단에 기전력이 발생하여 외부 회로에 전류를 흐르게 하는 것이다. 이러한 산소 이온 전도 특성이 고체산화물 연료전지의 작동 온도 및 성능을 결정하는데 핵심적인 역할을 하므로, 전해질은 고체산화물 연료전지의 핵심 부품인 셀 중에서도 가장 중추적인 역할을 하는 부분이라 할 수 있다. 고체산화물 연료전지에서 이상적인 전해질은 공기와 연료가 혼합되지 않도록 치밀해야 하고 산소이온 전도도가 높고 전자전도도가 낮아야 한다. 또한, 전해질은 양쪽에 산소 분압차가 아주 크기 때문에 넓은 산소분압 영역에서 위의 물성을 유지해야 한다. 최근의 연구 경향은 소재 원가 절감 및 장기 안정성 향상을 위해 작동 온도를 낮추려 하는 것이 핵심이다. 그러나 작동온도가 낮아질수록 고체전해질의 이온전도 특성이 급격히 저하되므로 이를 해결하기 위해 전해질을 박막화 하는 등의 공정기술 및 구조 개선을 통해 전해질의 저항을 낮추어 저온에서의 이온 전도 특성을 확보하려는 연구와 저온에서도 이온전도가 큰 전해질 재료를 개발하는 방향으로 연구가 진행되어 왔다.
가장 많이 사용되는 고체산화물 연료전지용 전해질은 이트리아 안정화 지르코니아(yttria-stabilized zirconia; YSZ) 재료이다. 그 외에도 최근에는 저온작동용 고체산화물 연료전지의 개발을 위해 전도성이 우수한 ScSZ(Sc2O3-stabilized ZrO2), 희토류 원소가 첨가된 CeO2(doped CeO2)계와 LSGM((La,Sr)(Ga,Mg)O3)계의 대체 전해질 연구도 활발히 이뤄지고 있다. 지금까지 알려진 산화물 고체전해질 재료 중에서 가장 높은 이온전도도를 보이는 것은 Bi2O3계 전해질이나 이 소재는 환원 분위기에서 열역학적으로 불안정해지므로 전해질 영역이 매우 좁은 것이 단점이다. 따라서 이를 극복하기 위해 다른 전해질 물질의 복합화 또는 다층 구조의 전해질을 적용하려는 노력이 계속되고 있다. 현재까지 연구되어 온 전해질 소재들의 전기전도도를 <그림 3-3-1-7>에 정리하였으며, 이하의 절에 각각의 전해질 소재의 장·단점 및 연구 동향에 대해 설명하도록 하겠다.
가. 지르코니아계 전해질 재료
지르코니아계 전해질 재료는 이후 개발된 타 전해질 재료들에 비해 상대적으로 이온전도도가 높지 않음에도 불구하고, 넓은 산소분압 하에서의 전해질 특성이 안정하며 화학적으로도 비교적 안정하다. 또한, 기계적 특성이 우수하며 가격도 비교적 저렴하여 현재까지도 가장 많이 사용되고 있고 일부 상업화에도 성공한 소재이다. 그러나 상대적으로 낮은 이온전도도로 인해 작동 온도가 800℃ 이상이 되어야 사용 가능한 것으로 알려져 왔으며, 낮은 온도에서의 작동을 위해 전해질을 보다 박막화 하거나 이를 신물질로 대체하기 위한 연구가 최근까지 활발히 진행 중이다. 안정화 지르코니아는 산소센서와 같은 분야에 산소이온 전도체로 가장 많이 이용되어 왔다. 순수한 ZrO2는 상온에서 단사정계(monoclinic) 구조이며 1,170℃ 이상에서 정방정계(tetragonal) 구조, 2,370℃ 이상에서 입방체(cubic) 구조를 갖는다. 이때 tetragonal-monoclinic 전이시 약 5%의 부피 변화가 생기게 되며 이를 막기 위해 CaO, MgO, Y2O3, Sc2O3 등의 첨가물을 첨가하여 안정화시키게 된다. 이러한 첨가물들은 ZrO2를 cubic 구조로 안정화시킬 뿐만 아니라, 산소 빈자리를 생성시키게 된다. 이렇게 증가한 산소 빈자리에 의해 산소 이온의 이동도가 증가하게 되며 산소 이온전도성이 생기게 된다. Y2O3를 첨가한 경우에 대하여 산소 빈자리가 생성되는 반응식을 기술하면 다음과 같다.
안정화 지르코니아는 첨가물의 종류와 양에 따라 전기전도도가 변화하며, 일반적으로 첨가물의 양이 증가함에 따라 전기전도도가 증가하다가 최고점을 보이고 감소하는 경향을 나타낸다. 전기전도도의 증가는 산소 빈자리의 양이 증가하면서 생기는 현상으로 설명할 수 있으며, 첨가량이 계속 증가하면서 생기는 전기전도도의 감소는 defect ordering, vacancy clustering, electrostatic interaction 등으로 설명된다.
안정화 지르코니아의 최대 이온전도도는 큐빅 상의 경계면 근처에서 일어나는데 가격과 실용성 등의 문제로 일반적으로 Y2O3가 8mol% 첨가된 지르코니아(8YSZ)가 사용되고 있다. 현재까지 개발된 모든 안정화 지르코니아들 중에서 가장 높은 산소이온 전도도를 보이는 물질은 Sc2O3가 고용된 경우이다. 이는 기존 YSZ 재료에 비해 약 2배의 산소이온 전도도를 가지고 장기 내구성도 더 우수하여 5,000시간 경과 후에도 열화가 없는 것으로 알려져 있다. 또한, 기계적 강도와 열팽창계수 등도 기존 YSZ 재료와 동일하여 기존에 활발히 개발되어온 전극 및 연결재 재료 등을 적용하기 쉽다는 장점이 있어, 이를 이용한 소재와 스택도 미국, 일본, 유럽 그리고 최근에는 중국 등에서 적용 연구를 활발히 진행 중이다.
나. CeO2계 전해질 재료
순수 CeO2는 이미 cubic 구조를 가지고 있으므로 구조를 안정화 시킬 필요가 없다. 또한, CeO2 내에서 Ce4+ 이온의 반경은 상당히 커서 다양한 종류의 첨가제로서 고용체를 형성할 수 있다. CeO2 계 산화물은 Gd3+ 및 Sm3+와 같이 Ce4+보다 가전자 수가 적은 원소를 첨가함으로써 산소 빈자리를 형성하여 산소이온 전도도를 가지게 된다. 특히 이온전도도가 지르코니아계 산화물보다 높아 500℃ 정도의 중온영역에서도 사용할 수 있는 대체 고체전해질로서의 사용 가능성이 연구되어 왔다. 그러나 중온영역에서는 산소 이온의 이동을 가능하게 하는 산소이온 빈자리와 이 산소이온 빈자리를 생겨나게 하는 첨가물 이온 사이의 전기적 인력이 작용하여 defect association을 형성시켜 산소이온 전도도를 저하시키기 때문에, 가능한 이 인력이 작은 첨가제를 선택하여야 한다. 이러한 인력은 첨가되는 이온들의 이온반경에 의존하며, Ce4+와 유사한 이온반경을 가지는 Sm3+, Gd3+, Y3+ 등의 이온이 주로 첨가물로 사용된다. Doped ceria는 고온과 낮은 산소분압하(고체산화물 연료전지의 연료극인 환원 분위기)에서 CeO2-x(0≤x≤0.5)로 환원되어 전자전도성을 나타내어 전해질로서의 단점을 가지고 있다. 최근에는 주로 연료전지의 공기극에서 안정한 산소이온 전도체인 2중 전해질로 사용하려는 연구가 진행되고 있다. CeO2계 전해질의 경우 특히 타 전해질보다 화학적 안정성이 상대적으로 우수하여, 이온전도도를 유지함과 함께 전극과의 화학적 반응을 억제하는 기능층으로의 사용을 위한 연구가 활발히 진행되고 있다. 그러나 이 시스템은 단독적인 전해질로 사용되기에는 아직까지는 한계를 나타내고 있으며 계속적인 연구가 필요한 실정이다.
고체산화물 연료전지, 차세대 분산발전용 기술 각광
국내 기술 세계 최고대비 80%, 産硏 상생협력 절실
다. Bi2O3계 전해질 재료
순수한 Bi2O3는 730℃ 이상에서 ZrO2와 같은 cubic 구조(δ-Bi2O3)를 가지며, 산소 부격자(sublattice) 자리 중 25%가 비어있다. 이러한 구조의 δ-Bi2O3는 현재까지 연구된 고체전해질 계열 중 가장 높은 산소이온 전도도(800℃에서 2.3S/cm)를 가진다. 그러나 730℃와 825℃(융점) 사이의 좁은 온도 범위에서만 안정하고, 730℃ 이하에서는 monoclinic상(α-Bi2O3)으로 전이하게 된다. 상전이에서는 큰 부피 변화가 일어나고 이로 인해 열 사이클에 의한 기계적 물성이 변한다. Bi 자리에 양이온을 치환하면 저온에서도 δ상을 안정화 시킬 수 있다. 22~27mol% WO3, 25~43mol% Y2O3 혹은 35~50mol% Gd2O3를 치환시킴으로써 안정화 영역을 상온까지 낮출 수 있다. 그러나 안정화제를 넣으면 상안정성은 좋아지나, 전기전도도의 감소를 가져오게 되므로 안정화제의 종류에 따라 적정한 양을 첨가하여야 한다. Bi2O3계 전해질은 고체산화물 연료전지의 연료극에서 환원되어 쉽게 분해되므로 SOFC 전해질로 단독적인 사용은 매우 어려우며, 연료극 쪽의 표면을 YSZ나 얇은 SDC로 코팅하여 사용하고자 하는 연구가 진행되어 왔다. 그러나 매우 낮은 기계적 강도 및 타 구성 재료들에 비해 큰 열팽창 계수 등 극복해야 할 여러 문제점을 가지고 있어 단기간 내에 상용화 하기는 어려울 것으로 판단된다. 랩스케일에서의 연구에서는 최근 Er2O3 등 다양한 안정화 첨가 원소 조성 개발 및 다층 구조 공정기술 구현 등으로 600도 이하의 저온에서도 2.0 W/cm2 이상의 매우 높은 출력특성이 보고되고 있으며, 양극 구성요소 등으로의 적용도 기대되고 있다.
라. LaGaO3계 전해질 재료
ABO3의 화학식을 가지는 페로브스카이트(perovskite) 구조의 산화물은 A자리 또는 B자리에 여러 가지 양이온을 첨가함으로써 물성을 다양하게 만들 수 있다. 이러한 구조의 전해질로 최근 활발히 연구되고 있는 물질로 LaGaO3계 전해질이 있으며, A+3B+3O3 형태의 LaGaO3 에 2가의 양이온을 첨가함으로써 산소 빈자리를 형성시킬 수 있다.
A자리에 치환시킬 수 있는 양이온은 Ca2+, Sr2+, Ba2+ 등이 있으며, B자리에는 주로 Mg2+를 주로 치환한다. 이들 2가의 양이온은 산소 빈자리를 형성시켜 산소이온 전도도를 향상시키지만, 10~20mol%에서 최대값을 가진 후 감소하는 경향을 나타낸다. 일반적으로 사용되는 조성은 LSGM(La0.9Sr0.1Ga0.8Mg0.2O2.85)이며 600℃에서 10-2S/cm 정도의 산소이온 전도도를 나타낸다. 또한, LSGM계열의 전해질은 넓은 산소분압에 걸쳐 안정한 산소이온전도 특성을 보여 일반적인 연료극 분위기에서도 사용 가능한 것으로 알려져 있다. LSGM계는 전도도를 높이기 위해 Ga 위치에 Mg 이외에 Co, Fe 등을 치환 고용시키기도 하며(대표적인 예: La0.8Sr0.2Ga0.8Mg0.1Co0.1O2.815), 이 경우 전기전도도가 증가하는 것으로 알려져 있다(Co를 치환할 경우 가장 전기전도도가 높다). Co가 도핑된 LSGM(LSGMC)의 경우 Co 함량이 증가함에 따라 전자전도성이 나타나기 때문에 8.5mol%가 적합한 것으로 알려져 있으며, LSGM에 비해 낮은 전압 특성을 보이나 전력밀도는 더 큰 것으로 알려져 있다.
LSGM을 SOFC용 산소이온 전도체로 사용하기 위해서는 전기적 특성뿐만 아니라 전극 등 타 구성 재료와의 화학적 친화성도 고려해야 한다. 예를 들면 셀 제조온도에서 음극 재료의 구성요소인 니켈이 LSGM과 반응하여 연료극/LSGM 계면에서 산소이온 전도성을 가지지 않는 물질인 LaNiO3상이 생성될 수 있다. 또한, 기존의 YSZ 전해질과 함께 사용하는 LaSrMnO3(LSM)과 LaSrCoO3(LSC)계 공기극 재료는 LSGM 전해질 재료와 상호 반응할 수 있다. 이러한 문제를 해결하기 위해 Sm0.2Ce0.8O1.9(SDC) 또는 La0.4Ce0.6O1.8(LDC)를 연료극 위에 박막 형태로 코팅하는 구조가 알려져 있다. LSGM 재료의 전극과의 반응성 및 높은 소결 온도 등에 의해 따라서 현재까지 LSGM계 전해질을 이용한 단전지는 대부분 전해질을 단독으로 소결한 후 전극을 상대적으로 낮은 온도에서 코팅하여 제조하는 전해질 지지형 구조로 제조되고 있다.
■ 기후변화대응 관점에서 기술의 중요성
정부는 지난 2015년 6월 국무회의를 통해 2030년까지 국가온실가스 감축 목표를 기존 30%보다 강화된 “배출전망치(BAU)” 대비 37% 감축으로 결정하였다. 또한, 그간 온실가스 감축에 소극적이던 미국 오바마 정부도 2030년까지 이산화탄소 배출량을 2005년 대비 32% 감축하기로 하고 8월 3일 이를 실천할 청정전력계획(Clean Power Plan)을 발표한 바 있다. 이러한 국제사회의 움직임 속에서 정부의 온실가스 감축 목표를 실현하고 산업계에 미치는 부담을 경감시키기 위해서는 온실가스 저감효과가 큰 기술, 그중에서도 기업이 개발하기 어려운 차세대 원천기술개발에 대한 정부 지원이 무엇보다 시급한 실정이다.
정부에서는 효과적인 온실가스 감축과 화석연료 기반 산업과의 시장 경쟁력 격차 해소를 위해 시장전망 및 기술경쟁력 등을 분석하여 6대 기술을 선정하였다(태양전지, 연료전지, 바이오에너지, 이차전지, 전력IT, 온실가스 포집처리). 이와 더불어 기술시장을 시장성숙도에 따라 미래, 초기, 성숙시장으로 나누어 시장에 따른 지원을 하고 민관 협업 생태계를 조성하려 하고 있다. 이를 통해 핵심기술 분야의 온실가스를 1,300만 톤 줄이고 선진국 대비 기술 수준을 2020년까지 93%로 증진시키며, 친환경 차량, 신소재 산업 등 신시장 창출 기반을 조성하는 것을 목표로 하고 있다. 기후변화 대응은 현실로 다가온 문제이며, 관련 원천기술 확보로 위험은 줄이고 기회를 늘릴 수 있다. 특히 도입 성장기 기술이 대부분인 관련 기술 특성상 세계시장 선점이 가능한 핵심기술과 산업모델 개발이 필요할 것으로 판단된다.
고체산화물 연료전지는 현재까지 개발된 에너지기술 가운데 가장 높은 효율을 보이는 발전 기술이다. 이로 인해 이산화탄소 저감 효과가 뛰어나 차세대 분산 발전용 연료전지 기술로 각광 받고 있다. 고체산화물 연료전지 기술은 기술적 난도가 높아 다른 형태의 저온 연료전지에 비해 기술 개발 시점이 늦었으나, 선진국을 중심으로 각국의 집중적인 노력으로 기후 변화대응 분산발전용 시스템의 중심적인 역할을 수행하고 있다. 세계 각국은 기후변화에 대응하기 위해 국가 정책차원에서 고체산화물 연료전지 개발을 수행해 왔으며, 현재 미국, 일본을 중심으로 100~400kW급 고체산화물 연료전지 발전 시스템이 약 100㎿급 이상 설치되어 운영되고 있다. 가정용 소형 시스템의 경우 현재까지 1만 대 이상 보급되고 있는 상황이며 발전 효율은 대용량의 경우 55% 이상을 나타내고 있고 최고의 경우 약 70%의 발전효율을 보인다. 소형 가정용 시스템의 경우 45% 이상으로 획기적인 발전 효율을 나타내고 있으며 이산화탄소 저감면에서도 50% 이상의 저감율을 보이고 있다.
우리나라의 경우 상용 연료전지 효율 향상(120%) 및 제조비용 절감(50%), 차세대 연료전지의 발전효율(1.5배) 및 수명(2배) 획기적으로 개선하는 것을 목적으로 연료전지 분야의 기후변화대응 핵심기술개발 분야가 선정되어 연구 개발이 진행되고 있다. 현재 성숙시장으로 PEMFC 및 MCFC가, 미래시장으로 SOFC 및 복합발전을 타깃으로 하고 각각 가격/품질경쟁 및 핵심기술 확보, 시장선점을 목표로 진행 중이다. 미래시장은 핵심기술 확보를 위한 R&D 집중투자가, 초기시장은 기술 상용화 촉진 및 시장 선점 지원을, 성숙시장은 민간의 가격 및 품질 경쟁을 측면 지원하는 것을 기본 골자로 하고 있다. 연료전지 성숙시장의 경우 선진국에 근접한 국내기술(세계최고대비 80% 이상)의 시장 경쟁력 강화를 위해 대기업-중소기업 간 및 기업-연구기관 간 상생 협력 활동을 지원하여 효율 120% 향상 및 제조비용 50% 절감을 목적으로 한다. 구체적으로는 백금촉매, 고분자 전해질 등의 고가소재를 대체할 수 있는 소재 및 부품 개선 연구를 지원하고, 창조경제혁신센터를 거점으로 하는 연료전지 산업 생태계 강화를 진행하며, 연료전지 산업의 조기 활성화를 위한 인프라 구축 및 시범사업 확대 등을 목표로 연구 개발이 진행 중이거나 진행될 예정이다.
차세대 연료전지 미래시장을 위해서는 기존 연료전지의 발전효율 및 수명을 획기적으로 개선하여 향후 세계시장을 선도할 수 있는 핵심기술 건에 대한 선제적 연구개발 추진을 목표로 한다. 구체적으로는 PEMFC 대비 생산비용이 50% 수준인 고체 알칼리 연료전지를 개발하고, 건물용 및 발전용 기존 연료전지를 대체할 고효율 고체산화물 연료전지를 개발하며, 연료전지-가스터빈 또는 연료전지-연료전지 복합발전시스템 기술개발로 발전효율 향상(70%) 및 발전원가 절감(33%)을 계획하고 있다. 특히 고체산화물 연료전지는 높은 효율로 이산화탄소 저감 효과가 뛰어나 차세대 분산 발전용 연료전지 기술로 각광 받고 있으며, 주로 발전효율을 높이고 수명을 늘리는 데 중점을 두고 연구개발이 추진되고 있다.
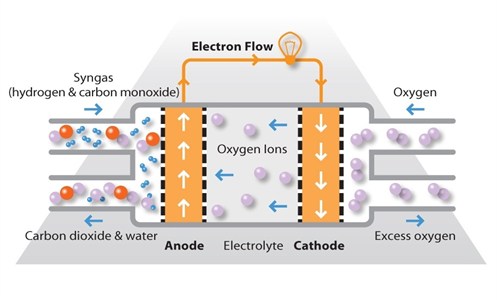
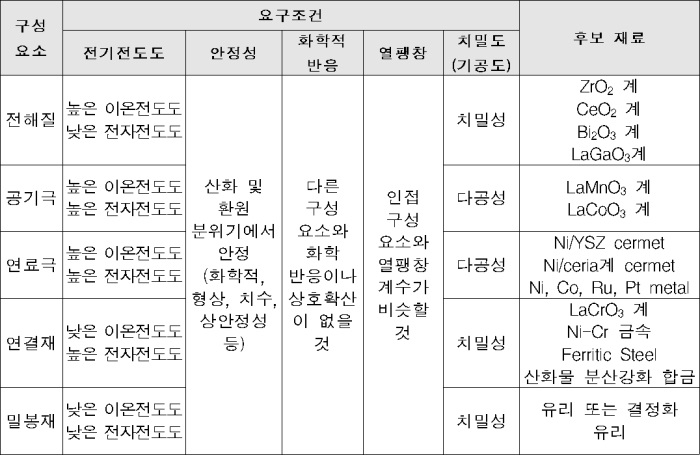
▲ <그림 3-3-1-4>제작형태에 따른 고체산화물 연료전지의 분류.
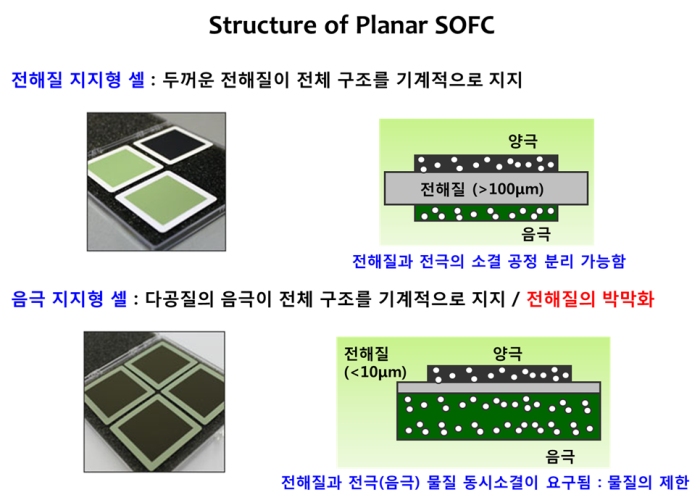
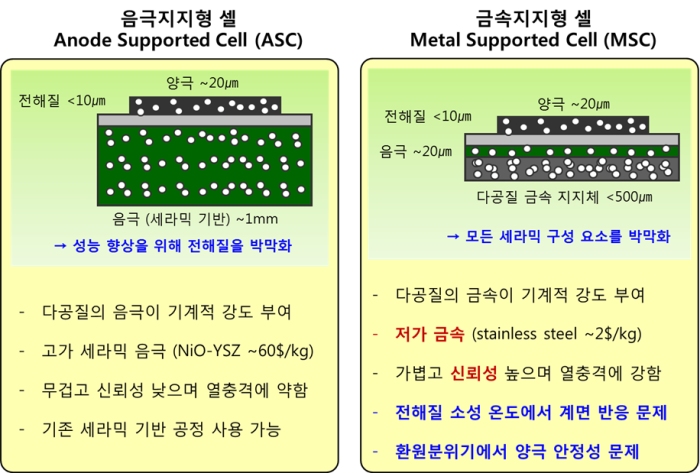
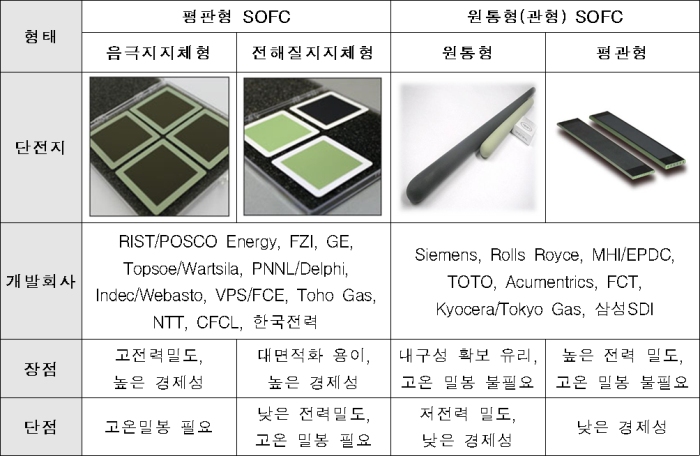
'Science, tech' 카테고리의 다른 글
KAIST, 연료전지 수명 연장 전극 코팅기술 개발 (0) | 2018.07.24 |
---|---|
美, 수소연료전지 선박 최초 개발한다 (0) | 2018.07.24 |
연료전지란? (0) | 2018.07.24 |
수소전기차와 전기차 (0) | 2018.07.24 |
혈관만 남기니 사람 꼴이 이렇게 보인다. (0) | 2018.07.06 |